Client’s request
Through the services of the European Digital Innovation Hub (EDIH) Northeast Bohemia project at the Regional Development Agency, increase productivity and optimise production processes. Specifically, the client needed help in selecting a suitable production information system and wanted to test the new system in real operation first, without having to invest fully in it immediately.
How we helped
The Turnov commercial foundry, which produces castings in aluminium and cast iron, was struggling with the fact that its production was dependent on the interconnectedness of individual departments. It was quite difficult to reconcile several departments headed by several masters. First, an analysis of the needs in production was carried out and a proposal for potential improvements through digitalisation was drawn up. The goal was to help with data collection so that the client could determine which areas of production could get the biggest improvements at the least cost.
By implementing a new manufacturing information system (MES), the client streamlined worker and machine utilization during a three-month trial period, which, combined with better workplace connectivity, reduced downtime and increased productivity by 6-10 %.
The newly implemented production information system can present a true picture of time and machine utilization to management and provide them with the basis for ongoing implementation of corrective measures.
Funding
Thanks to the Test Before Invest financing scheme, the client had 70% of the installation, service, license, cloud rental, training and customization of the interface to specific requirements for three months.
Who we worked with
The Regional Development Agency through the European project EDIH Northeast Bohemia and our team (Zdeněk Runštuk, Jiří Vojtěch) with the management of the Turnov Commercial Foundry (Pavel Světlík) and the external supplier of the manufacturing information system (MES), Softli (Lukáš Slovák).
References
“Aligning multiple departments headed by multiple foremen was quite difficult for us. We used the company planning system OPTI to monitor the production processes, and then Excel, paper and pencil. The newly implemented system from the Regional Development Agency, conveniently through the European Digital Innovation Hub Northeast Bohemia project, can present us with a true picture of the use of working hours and machines and give us the basis for the ongoing implementation of corrective measures by the management.”
Pavel Světlík, Director of the Turnov Commercial Foundry



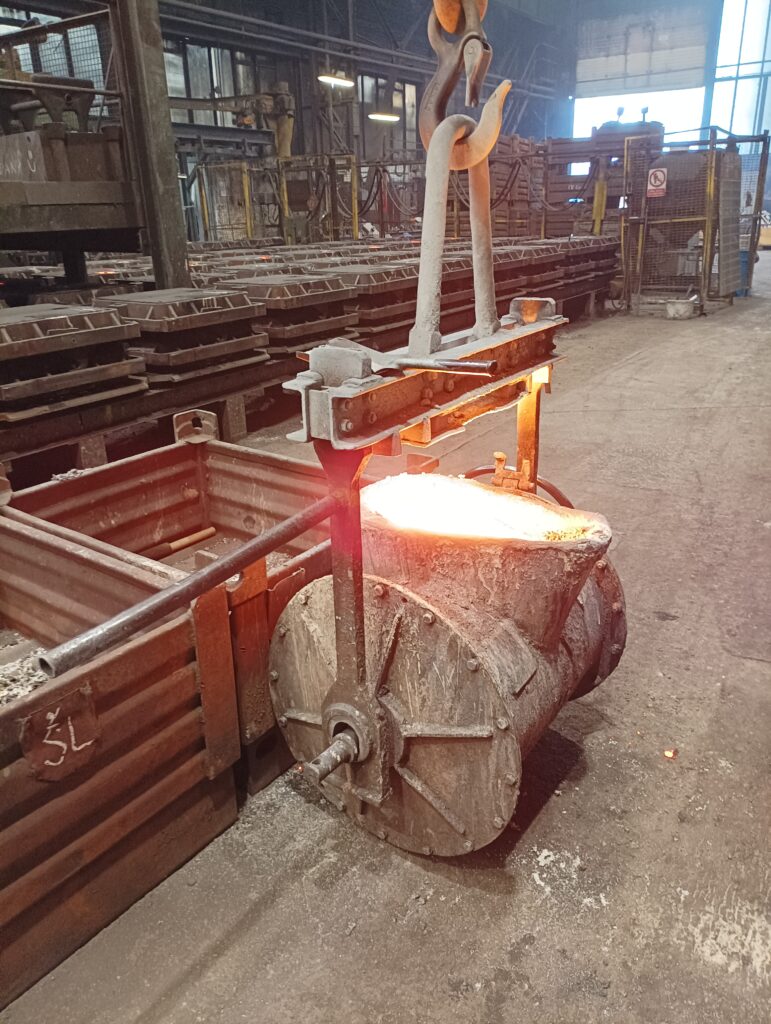
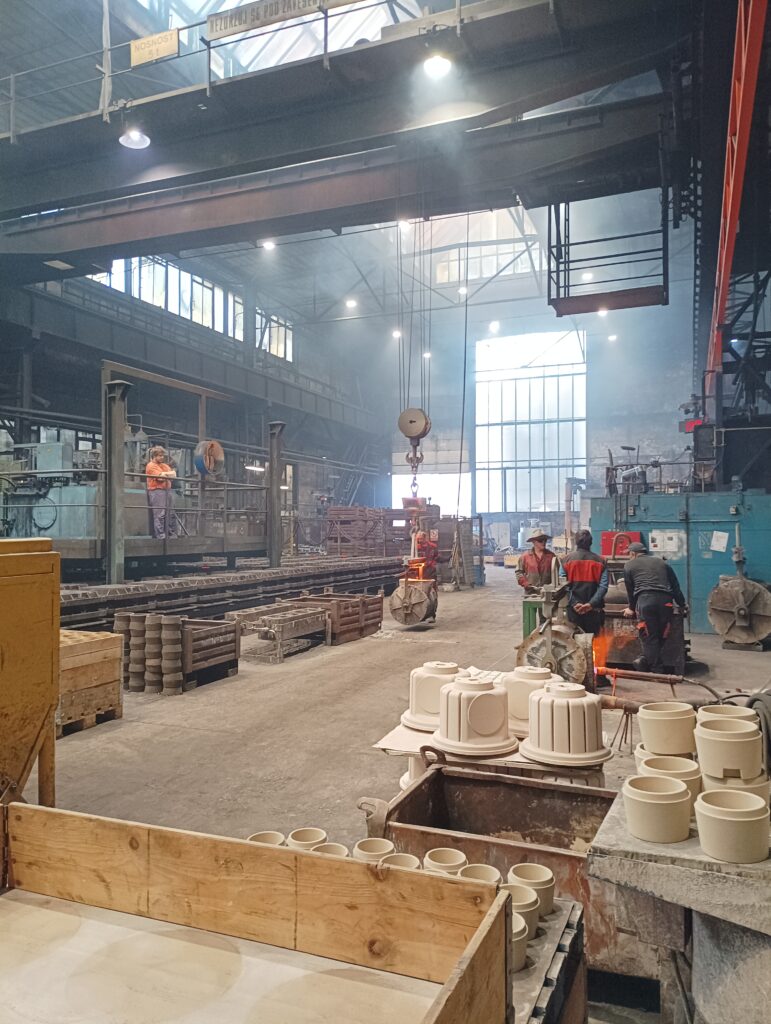
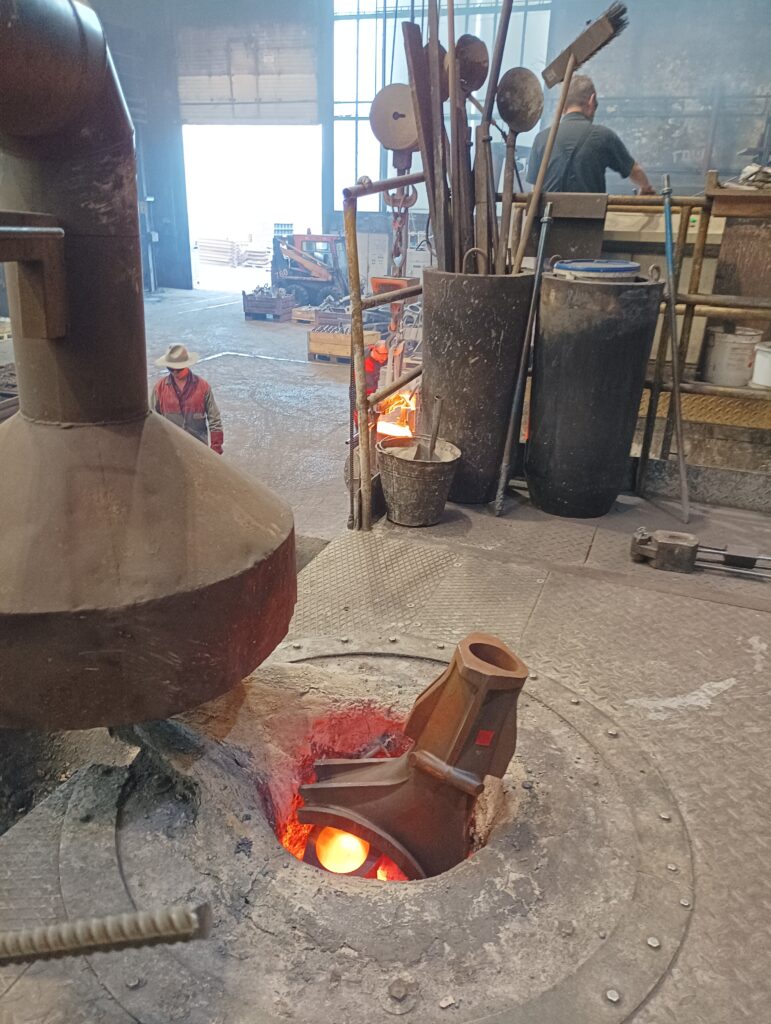
More information
- https://liberecka.drbna.cz/zpravy/spolecnost/36616-male-firmy-se-boji-promarnene-investice-turnovska-slevarna-si-tak-nove-technologie-nejprve-zkousi.html
- https://www.casopisczechindustry.cz/products/diky-digitalizaci-zvysila-turnovska-slevarna-produktivitu-o-10
- https://www.ceske-novinky.cz/2024/07/13/diky-digitalizaci-zvysila-turnovska-slevarna-produktivitu-o-10
- https://www.ceske-novinky.cz/2024/07/13/diky-digitalizaci-zvysila-turnovska-slevarna-produktivitu-o-10/
- https://feedit.cz/2024/07/11/diky-digitalizaci-zvysila-turnovska-slevarna-produktivitu-o-10/